In the fast-evolving landscape of manufacturing, CNC milling technology stands as a cornerstone of precision and efficiency. As industries seek to enhance their capabilities, the drive for innovation has birthed groundbreaking advancements that redefine the boundaries of what’s possible.
Among the myriad of developments emerging, three particular innovations are making waves, poised to transform traditional CNC milling into a more agile and sophisticated endeavor. From automation enhancements that streamline operations to cutting-edge materials that improve performance, these trends promise to elevate the standards of quality and speed in manufacturing.
Buckle up as we delve into these exciting innovations that are set to reshape the future of CNC milling.
Advancements in Adaptive CNC Technology
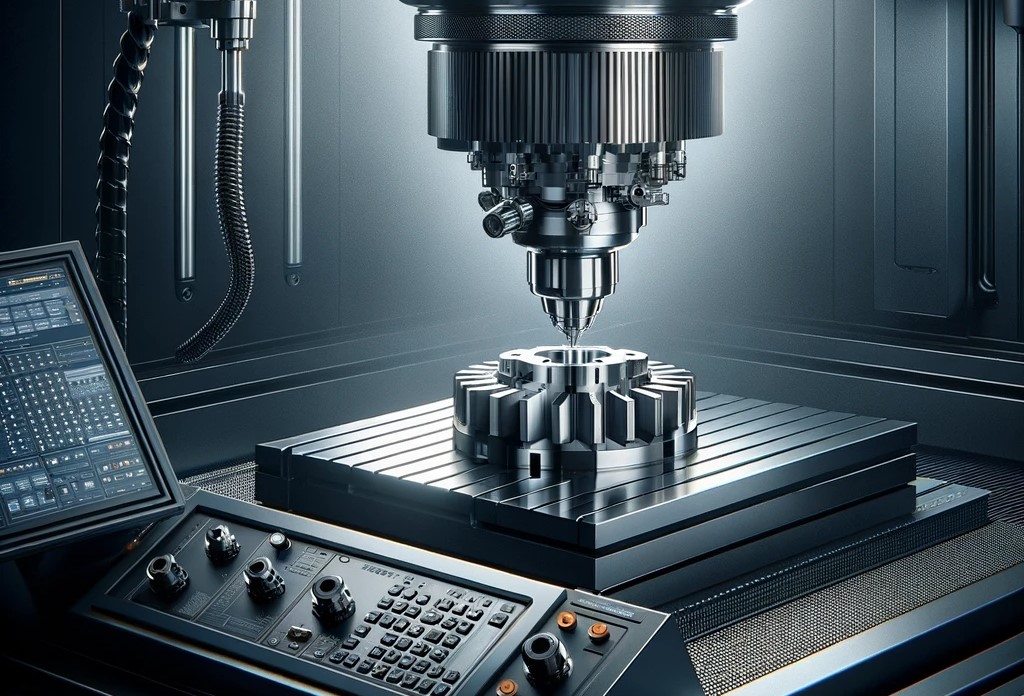
Recent advancements in adaptive CNC technology have transformed the landscape of milling manufacturing, pushing boundaries that were once thought insurmountable. Imagine machines that learn and adjust in real-time—this is no longer a futuristic dream but an evolving reality.
With the integration of artificial intelligence and machine learning algorithms, CNC systems can now analyze variances in material properties or machine conditions on the fly, optimizing cutting parameters to enhance precision and efficiency. This dynamic capability not only minimizes waste but also prolongs tool life, resulting in significant cost savings.
Furthermore, intuitive user interfaces and cloud connectivity empower operators with unprecedented access to data analytics and remote diagnostics, enabling smarter decision-making. In a world where time is of the essence, adaptive CNC technology emerges as a game-changing cornerstone, paving the way for unparalleled productivity and innovation in the industry.
Integration of Artificial Intelligence in CNC Operations
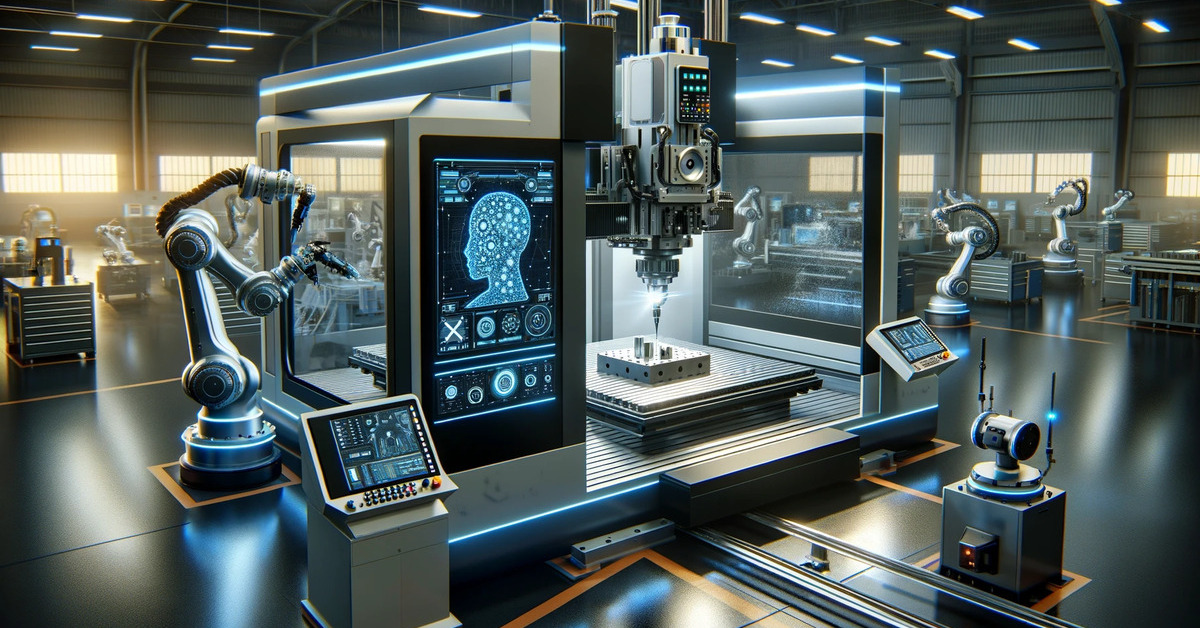
The integration of artificial intelligence (AI) into CNC operations marks a revolutionary leap in manufacturing precision and efficiency. By harnessing machine learning algorithms, manufacturers can now optimize tooling paths and predict maintenance needs with remarkable accuracy.
Imagine a milling machine that not only responds to real-time data but also learns from previous operations, adapting its performance to enhance productivity. This symbiotic relationship between human ingenuity and AI capabilities allows for a dynamic workflow where errors are minimized, and production times are significantly reduced.
Furthermore, with AI-driven analytics, operators can make data-informed decisions on the fly, ensuring that even the most intricate designs are executed flawlessly. As CNC machines become smarter, the landscape of manufacturing transforms, paving the way for unprecedented innovation and competitiveness in the industry.
The Rise of Hybrid Manufacturing Techniques

The landscape of cnc milling manufacturing is undergoing a transformation, driven by the rise of hybrid manufacturing techniques that seamlessly integrate additive and subtractive processes. Imagine a world where 3D printing capabilities merge with traditional milling; this synergy creates unparalleled opportunities for innovation.
Manufacturers are now able to craft intricate geometries with exceptional precision, utilizing additive methods to build up materials layer by layer, followed by milling to achieve the desired finish. This convergence not only enhances design flexibility but also reduces waste, as excess material can be minimized through intelligent layering.
As industries increasingly demand complex components with tighter tolerances, hybrid manufacturing stands at the forefront, heralding a new era of efficiency and creativity in the CNC milling sector. Its a fascinating time, where each new advancement pushes the boundaries of what’s possible, captivating engineers and manufacturers alike.
Conclusion
In conclusion, the landscape of CNC milling manufacturing is rapidly evolving, driven by groundbreaking innovations that enhance precision, efficiency, and versatility. The introduction of advanced materials, automation through AI-driven tools, and the integration of IoT technologies are setting new benchmarks for productivity and quality.
As these innovations continue to unfold, they not only promise to streamline manufacturing processes but also to open up new avenues for creativity and customization in machining. Embracing these advancements will be crucial for companies aiming to remain competitive in an increasingly fast-paced industry.